Shaping/Welding
Hands-on time for projects (the majority of the day)
Brief discussion of major principles of days 1 & 2
1. Welding, resmelting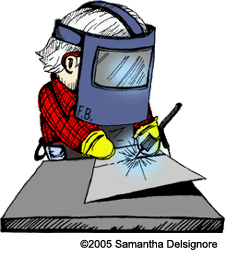
- Controlling chemistry of the puddle
- Eliminating surface oxides and contaminants
- Getting the right heat in the right amount in the right area
- Planning for the shrinkage due to temperature differential
2. TIG, MIG, Oxy-acetylene, Stick
- Preparing for welding – repair
- Why failure – over stressed/corrosion
- Cleaning up of part – prep of joint – “v” of root
- New fabrication – joint/seam placement – parameters for such
- What is base material – what alloy – what rod alloy – what effects elements have – melting/boiling/reactive
- Choosing weld process – TIG/MIG – speed, deposition, integrity, soundness
3. What is happening during welding
- Grain growth – shrinkage – temperature gradients in heat affected zone
- Parameters – fillet/weld size and configuration – advantages – what to look for – why use filler metal – how much to add
- Common problems, weld discontinuities and defects - cooling rates – contaminates – undercuts – porosity – hot tear – alloy problems – inclusions – lack fusion
- How to correct – effects of preheat – how to determine proper temperature – how different weld methods effect need for preheat
4. TIG process – Highlight constant current (amp) machines
- TIG tungsten: selection of size/type – amount current carried – welder settings, effect on if contaminated – how to prepare
- Gas flow – amount and different types of gases
- Setting up TIG station , what is “square wave”
- Understanding all settings on TIG power sources, electric current and polarity, high frequency
- How to adjust modern inverter welding power sources – asymmetrical wave forms
5. Welding light protection
- ANSI 787.1 approval UV-IF rays and nonionized radiation
- Color vs. temperature – oxide layers and light rays
Day 1 Day 2 Day 3
|